Working parameters Flex Hones
Brushes for deburring, edge rounding, surface finishing.
Ideal for use on CNC machines, transfer machines, automatic machines, robotic cells…
Shank with cylindrical or Weldon attachment and internal cooling
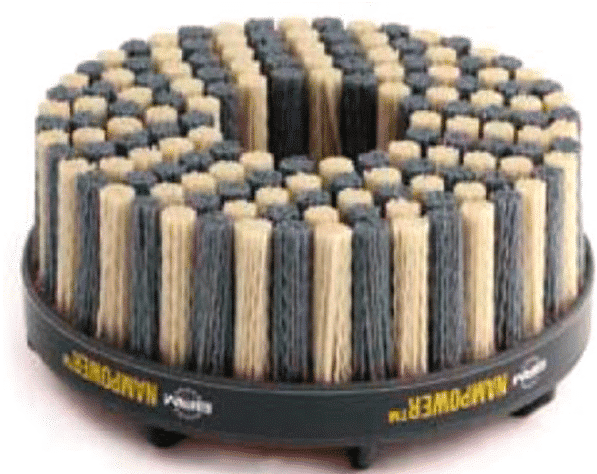
Dot
Generic use in deburring and finishing
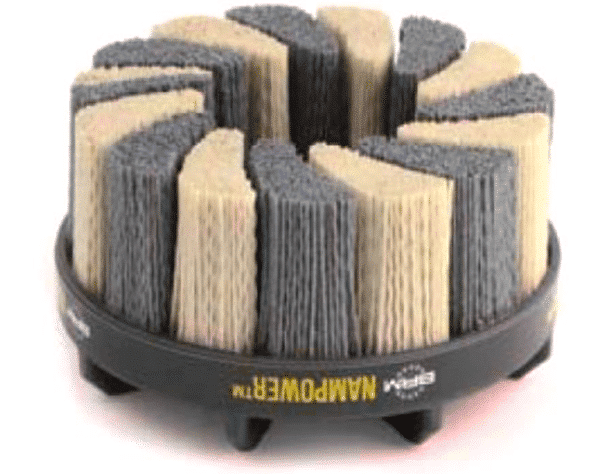
Turbine
Applications for medium to heavy deburring
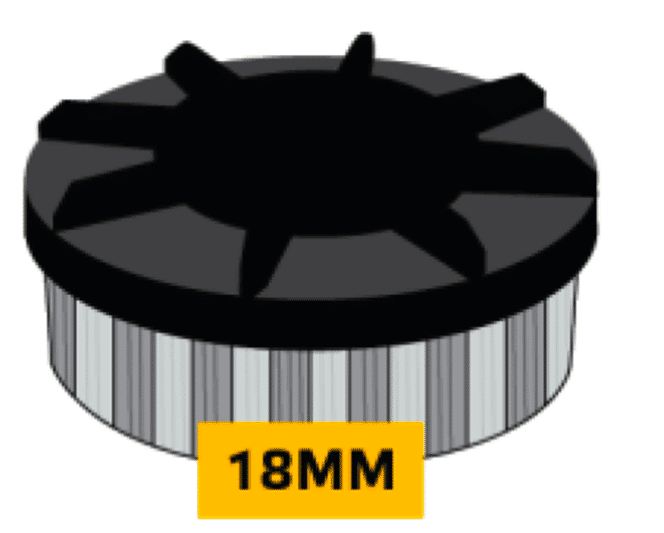
18mm bristles
Less flexibility, higher aggressiveness
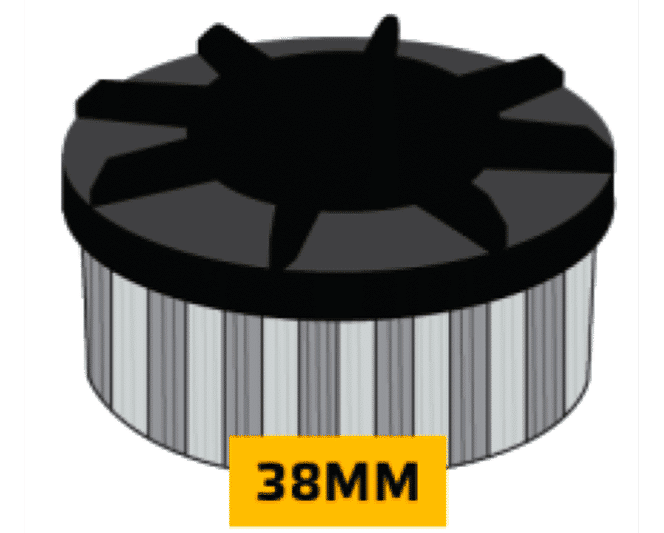
Filamenti 38mm
maggiore flessibilità,
minore aggressività
Brush Diameter
Surface coverage
The brush should ideally be approximately 25mm larger than the part being worked on. If a smaller brush is required due to space constraints, the centerline of the brush should be aligned with the edge to be deburred with a minimum of 35-40mm overlap between passes.
Tool path
The brush should start rotating immediately at the working speed given for its diameter, and it should begin and end the path completely outside of the part.
Rotation direction
The brush should rotate in the opposite direction of the cutting tool that created the burr
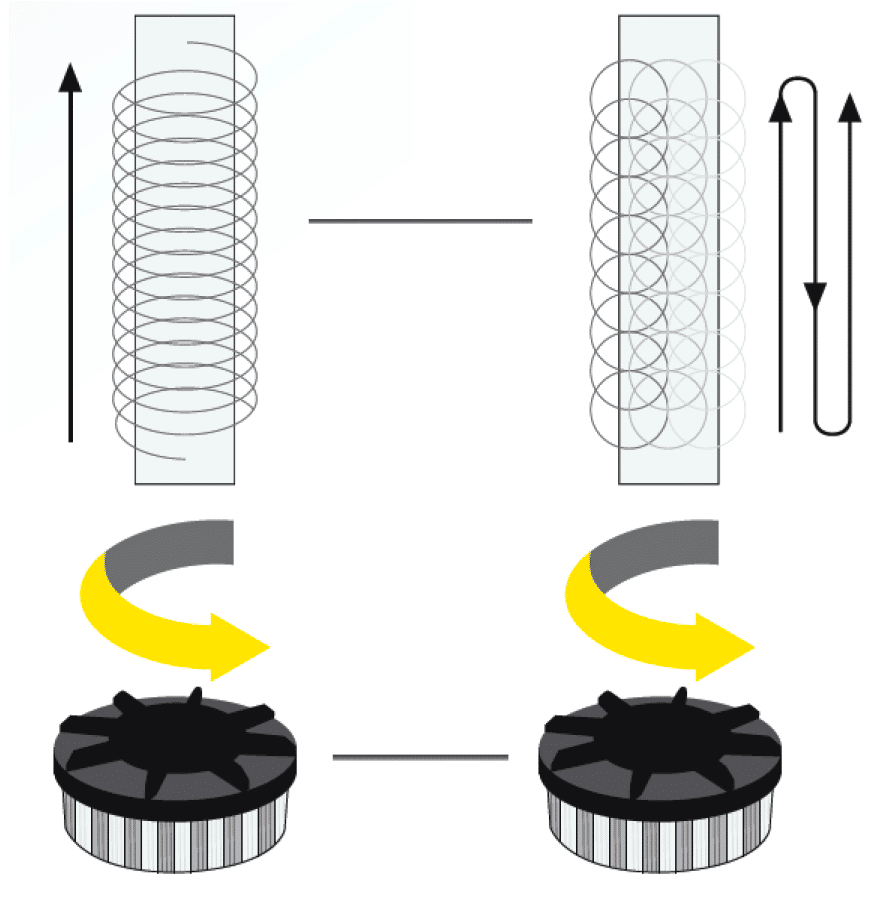
Grit
The choice of grit depends on the required finish value. The general rule is to choose the coarsest grit that can maintain the required finish. Using a fine grit on a surface with a high starting finish (Ra) produces a worse result than using a coarse grit followed by a fine one. Coarse grits are recommended for heavy deburring where an extremely low Ra surface finish is not required.
Grit | Starting Ra |
80 | 1.3-1.5 |
120 | 1.0-1.3 |
180 | 0.8-1.0 |
320 | 0.5-0.8 |
Recommended and Maximum Working Speeds
The brushes should be used at a lower speed than the maximum indicated to prevent overheating and melting of the nylon on the working surface. It is recommended to stay below 760 m/min for dry use and below 1,070 m/min for wet use. A 150 mm diameter brush used at 1,400 rpm is more effective than the same brush used at 2,800 rpm. Excessive speed, especially with a long filament length, causes deformation and bouncing of the filaments. Typically, brushes are used at higher speeds to prioritize aggressiveness and at lower speeds to prioritize the brush’s adaptation to the surface’s contour..
Diameter mm |
Grit – rpm |
Max rpm |
|||
#80 | #120 | #180 | #320 | ||
50 | 6.500 | 6.250 | 4.000 | 3.500 | 6.500 |
60 | 5.500 | 5.000 | 4.000 | 2.750 | 5.500 |
80 | 4.500 | 4.250 | 3.500 | 2.500 | 4.500 |
100 | 1.850 | 1.800 | 1.750 | 1.700 | 2.200 |
125 | 1.600 | 1.550 | 1.500 | 1.450 | 2.000 |
150 | 1.350 | 1.300 | 1.250 | 1.200 | 1.800 |
Cutting pressure
The cutting pressure should be adjusted to 10% of the bristle length for small-section (#320) and no more than 5% for larger-section bristles (#80-120-180). The higher the cutting pressure, the lower the rotation speed should be so that the filaments can adapt to the shape of the part.
DOT | TURBINE |
0.4-3.8 mm | 0.1-2.4 mm |
Feed Rate
The feed rate depends on various factors such as the size of the burrs, material, surface contour, and required finish. Flat surfaces are processed at high speed and low cutting pressure, while curved surfaces with variations in level are processed at low speed and high cutting pressure. The recommended feeds are a starting point, but the most effective feed depends on the application and should be determined through processing trials.
Material | m/min |
Non Ferrous | 2.00 m/min |
Cast iron | 1.50 m/min |
Ductile Steel | 1.25 m/min |
Stainless and alloyed steel | 0.75 m/min |
Titanium and alloys with high Nichel content | 0.75 m/min |
Wear Compensation
Some machines allow monitoring the spindle load and adjusting the cutting pressure to maintain a constant value. In most CNC machines, there is an automatic increment determined by wear detected in processing trials or through brush height control or manual adjustment.
Suggestion
More aggressiveness
- Short bristles
- Larger brush diameter
- Coarser grit
- Higher bristle density
- Higher rotation speed
- Higher cutting pressure
Less aggressiveness
- Long bristles
- Smaller brush diameter
- Finer grit
- Lower bristle density
- Lower cutting pressure
Non planar surface
- Long bristles
- Finer grit
- Lower bristle density
- Higher cutting pressure
High finish required
- Use coolant
- Long bristles
- Higher rotation speed
No finish required
- Use dry
- Coarser grit
- Smaller brush diameter
- Lower rotation speed
To prevent melting of the bristles
- Use coolant
- Smaller brush diameter
- Lower rotation speed
- Lower cutting pressure